Belt Tool
-
OEM belt tooling cost $180 each and four are required per machine
-
Current solution: screwdrivers wedged into belt
-
Solution: created alternative in house tooling using 3D printing
-
Result: $10 per tool, costing $20,000 total for the machine family
Belt Tool Project Scope
My job often had me being approached by SMEs with problems they needed solved. In this case it was a belt tool that was crazily expensive for what it was. The tool was a simple 3 stack of sheet metal with a slot in the teeth, similar to the 3D oriented one I have here. They were charging $180 per unit. With 4 per machine, that is $740. There are 500+ machines that use this belt. That is $360,000 in tooling for a machine family that one machine costs $50,000.
To begin with I acquired a belt module the tool was for. I then measured the gaps in it to mimic what the OEM did and created a set of 3D printed prototypes. I have one with me today.
We tested the prototype for form, fit, and function. The Prototypes did not fail at that point in time so we decided to move forward with a more conventional way of creating the tool. I reached out to my contact at the postal machine shop and communicated our requirements for the tooling, such as material. We settled on UHMW since the 3D printed version did not fail, we assumed the plastic version wouldn’t fail either. However after using the 3D printed versions in our lab environment, one failed as well as one of the UHMW versions.
At this point in time we discovered why the OEM part had the slot in it’s design. The OEM had updated the belting to the new version shown on the slide where they added a ridge of plastic in the middle of the slot. There was an incident where somebody had caught their fingers in it, this caused us to rethink how to make it. I then updated the design to this metal version as seen here which would fit into one of those slots and also be durable enough not to break.
I then communicated the change updates to the manufacturing unit for the Post Office and had them create a new set out of 11 gauge stainless steel since that would prevent corrosion and eliminate the need for a coating. This also ensured that the tools would fit well without the risk of over spray in the manufacturing process. We tested the new metal ones in the lab and they functioned perfectly. I then presented it to the postal customer for Mass producing and deployment Nationwide.
Some of the benefits of the final product is that it is universal in that it doesn't matter which way you put it into the machine making it easier to explain how to use it to operators. Again, it's stainless steel so you don't have to worry about corrosion and the gauge is a good fit. Meaning it can be made simply by laser cutting the general shape out.

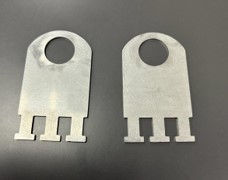